Ammonium Antimonate Production Cost: An In-depth Analysis of Market Dynamics
Ammonium Antimonate, a key compound used in various industries such as electronics, pharmaceuticals, and chemical manufacturing, plays a vital role in the production of semiconductors, flame retardants, and catalysts.

Ammonium Antimonate, a key compound used in various industries such as electronics, pharmaceuticals, and chemical manufacturing, plays a vital role in the production of semiconductors, flame retardants, and catalysts. Understanding the Ammonium Antimonate Production Cost is crucial for manufacturers, as it directly influences product pricing, profitability, and competitiveness. This article provides an in-depth look at the cost model, pre-feasibility, industrial trends, labor charges, utilities, logistics, supply chain, and lifecycle cost analysis involved in Ammonium Antimonate production.
Ammonium Antimonate Overview and Market Demand
Ammonium Antimonate (NH₄SbO₃) is primarily used in the production of flame retardants, semiconductors, and catalysts in industries such as electronics, automotive, and chemicals. Its demand is primarily driven by its role in manufacturing flame-retardant materials, especially in the growing electronics sector, where fire safety standards are stringent.
Request a Free Sample - https://www.procurementresource.com/production-cost-report-store/ammonium-antimonate/request-sample
Additionally, Ammonium Antimonate is a vital precursor in the synthesis of antimony compounds used for enhancing the performance of various materials. The growing demand for electronic devices, renewable energy solutions, and automotive safety is expected to drive the market for Ammonium Antimonate.
Given the increasing demand for this compound, understanding its production cost is paramount to improving efficiency, minimizing costs, and boosting profit margins. Ammonium Antimonate is a critical material for several high-demand industries, and its cost structure has a significant impact on manufacturers.
Ammonium Antimonate Production Cost Model
The Ammonium Antimonate Production Cost is determined by a range of factors, including raw materials, labor, energy consumption, and logistics. A detailed cost model helps manufacturers understand where they can optimize their operations to reduce expenses. Let’s explore the key components of the cost model:
1. Raw Material Costs
The primary raw materials required for Ammonium Antimonate production include antimony trioxide and ammonium salts. Antimony is a rare metal, and the cost of its procurement is influenced by mining activities, regional availability, and market demand. Prices for these raw materials can fluctuate, making it important for manufacturers to secure stable and cost-effective sources.
In addition to raw materials, the production of Ammonium Antimonate requires high-quality solvents, acids, and other reagents. These chemicals are subject to market price fluctuations and need to be sourced at competitive prices to maintain cost-effective production.
2. Labor Charges
Labor costs are another crucial component of the Ammonium Antimonate Production Cost. Skilled labor is required for tasks such as overseeing chemical processes, quality control, and managing the production lines. Labor charges can vary depending on the location of the manufacturing facility and the complexity of the production process.
Manufacturers that adopt automation and advanced manufacturing technologies can reduce their dependency on manual labor, helping to cut costs and improve production efficiency.
3. Utilities and Energy Consumption
The production of Ammonium Antimonate requires substantial energy input for chemical reactions, including heating, distillation, and purification processes. The cost of utilities such as electricity, water, and gas can significantly affect production costs. Energy consumption can be optimized through energy-efficient equipment, but in regions with high energy costs, these charges can be a major expense.
Manufacturers are increasingly looking at sustainable and renewable energy sources to mitigate utility costs and reduce their environmental impact, as energy-efficient technologies can contribute to long-term savings.
4. Logistics and Supply Chain Management
Logistics costs, including the transportation of raw materials and distribution of the final product, play an important role in the overall Ammonium Antimonate Production Cost. Efficient supply chain management helps to optimize costs associated with warehousing, transportation, and inventory management. Transportation costs can vary depending on the location of raw material suppliers, market demand, and global logistics infrastructure.
To maintain cost-efficiency, businesses must ensure that supply chains are streamlined and minimize transportation delays, inventory holding costs, and shipping inefficiencies.
Pre-feasibility for Ammonium Antimonate Manufacturing Plant
Before setting up a Ammonium Antimonate manufacturing plant, a pre-feasibility study is critical to assess the overall viability of the project. A thorough pre-feasibility report should take into consideration factors such as raw material availability, market demand, regulatory compliance, financial feasibility, and the expected return on investment (ROI).
Some important factors in the pre-feasibility phase include:
-
Raw Material Availability: Analyzing the availability and stability of raw material supply is essential for long-term production sustainability. Prices for materials like antimony trioxide can fluctuate, making it important to secure cost-effective suppliers.
-
Regulatory Compliance: Ammonium Antimonate production involves certain regulatory requirements due to its chemical nature. Compliance with environmental regulations, safety standards, and labor laws is crucial for maintaining business operations and avoiding legal complications.
-
Market Demand: Demand for Ammonium Antimonate is driven by industries such as electronics, automotive, and chemicals. A pre-feasibility study should evaluate market conditions and growth projections to ensure that the plant can meet future demand.
-
Capital Investment: The initial setup cost for an Ammonium Antimonate manufacturing plant involves capital investment in equipment, facilities, labor, and safety systems. A cost-benefit analysis is needed to determine if the plant’s projected returns will justify the initial investment.
Industrial Trends Affecting Ammonium Antimonate Production
The Ammonium Antimonate production industry is shaped by several key industrial trends. These trends are driven by changing market demands, technological advancements, and sustainability efforts. Some of the major trends include:
-
Sustainability: As industries push for sustainable manufacturing processes, companies are adopting more eco-friendly methods for producing chemicals like Ammonium Antimonate. Sustainable sourcing of raw materials, energy-efficient production techniques, and waste management systems help reduce environmental impact and production costs.
-
Technological Advancements: Innovations in chemical processing technologies are improving the efficiency and yield of Ammonium Antimonate production. Automation, artificial intelligence, and data analytics are helping manufacturers optimize processes, reduce waste, and enhance product quality, ultimately lowering costs.
-
Rising Demand for Flame Retardants: As regulations surrounding fire safety become more stringent, the demand for Ammonium Antimonate-based flame retardants has increased. This is especially true in the electronics and automotive industries, which require high-performance, fire-resistant materials.
-
Supply Chain Resilience: The global supply chain disruptions experienced in recent years have highlighted the need for more resilient and efficient logistics and supply chains. Manufacturers are investing in better inventory management, alternate sourcing options, and smarter distribution networks to reduce delays and cost fluctuations.
Lifecycle Cost Analysis of Ammonium Antimonate Production
The lifecycle cost analysis (LCA) is an essential tool for businesses to evaluate the total cost of Ammonium Antimonate production. LCA takes into account every stage of production, from raw material procurement to final product delivery. Analyzing the full lifecycle helps identify potential cost-saving opportunities and allows businesses to optimize production processes.
Key components of an LCA for Ammonium Antimonate include:
- Raw Material Sourcing: Evaluating the long-term cost of sourcing antimony trioxide and other chemicals necessary for production.
- Energy Usage: Analyzing energy consumption throughout the production process to identify opportunities for energy savings.
- Waste Management: Assessing waste generation and disposal costs, as well as opportunities for waste recycling or reuse.
- Packaging and Distribution: Evaluating the costs of packaging, shipping, and handling, and finding ways to optimize these expenses.
Request for Real-Time Prices
To stay competitive in the market, it is essential to request real-time prices for Ammonium Antimonate raw materials, energy, and logistics services. Tracking the latest price fluctuations allows businesses to adjust their procurement strategies, ensuring that they maintain cost efficiency and profitability.
For more detailed information or to request Free Sample – https://www.procurementresource.com/production-cost-report-store/ammonium-antimonate/request-sample
Procurement Resources for Ammonium Antimonate Manufacturing
Effective procurement management is critical for controlling production costs and maintaining a steady supply of raw materials for Ammonium Antimonate production. By leveraging procurement resources, businesses can secure reliable and cost-effective suppliers, monitor price trends, and optimize their supply chain strategies.
Some key procurement strategies include:
- Supplier Diversification: By sourcing antimony trioxide and other critical raw materials from multiple suppliers, businesses can reduce risk and secure the best prices.
- Cost Forecasting: Using procurement tools to track market trends and forecast price fluctuations, allowing businesses to plan ahead and lock in prices at favorable rates.
- Logistics Optimization: Streamlining logistics operations to reduce transportation costs, improve delivery timelines, and ensure smooth supply chain management.
Contact Us
Company Name: Procurement Resource
Contact Person: Amanda Williams
Email: sales@procurementresource.com
Toll-Free Numbers:
USA: 1 307 363 1045
UK: 44 7537171117
Asia-Pacific (APAC): 91 1203185500
Address: 30 North Gould Street, Sheridan, WY 82801, USA
What's Your Reaction?
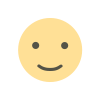
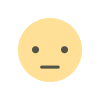


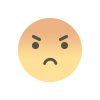
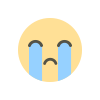
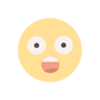