Essential Gas Turbine Maintenance Practices: Ensuring Optimal Performance

Gas turbines play a pivotal role in power generation and industrial applications, offering high efficiency and reliable performance. However, like any complex mechanical system, gas turbines require regular maintenance to ensure they continue to operate at peak efficiency. Neglecting proper upkeep can lead to reduced performance, higher operating costs, and even catastrophic failures. In this blog, we will explore essential gas turbine maintenance practices that help ensure optimal performance, increase longevity, and minimize downtime.
The Importance of Regular Maintenance
Gas turbines operate under extreme conditions, subject to high temperatures, fluctuating pressures, and constant mechanical forces. These challenging environments make regular maintenance crucial to ensuring the turbine functions optimally. Routine checks and servicing help maintain the integrity of turbine components, preventing them from operating below their efficiency potential, which can lead to excessive fuel consumption and reduced performance. By ensuring that the turbine is running smoothly, regular maintenance maximizes efficiency and minimizes energy waste.
Another significant benefit of regular maintenance is the extended lifespan it provides for turbines. Just as with any complex machinery, consistent upkeep prevents wear and tear that would otherwise shorten the life of critical components. Addressing issues before they become serious problems reduces the likelihood of costly repairs and parts replacements. In turn, this results in a longer operating life for the turbine, offering better return on investment for businesses.
Finally, regular maintenance plays a vital role in minimizing unexpected downtime. Turbines that undergo frequent inspections and proactive maintenance are far less likely to experience catastrophic failures. By identifying and resolving small issues before they escalate, companies can avoid costly unplanned outages and ensure continuous operation. Without these regular checks, turbines may suffer from degraded performance, increased fuel consumption, and even mechanical breakdowns, leading to significant repair expenses.
Key Maintenance Tasks
Inspections and Cleaning of Components
-
Air Filters and Inlet Systems: Regular inspection and cleaning of the turbine’s air filters are essential to prevent dirt and debris from entering the combustion chamber, which can cause damage or reduced efficiency.
-
Compressor and Turbine Blades: Over time, dirt, corrosion, and thermal fatigue can wear down compressor and turbine blades. Periodically inspecting these blades for cracks or erosion and cleaning them to remove buildup ensures optimal air intake and exhaust efficiency.
-
Combustion Chambers: Inspect combustion chambers for carbon build-up and perform cleaning to prevent reduced combustion efficiency.
Oil and Coolant Checks
-
Lubrication Systems: Gas turbines rely on lubrication to keep their moving parts functioning smoothly. It is crucial to regularly check oil levels, replace filters, and clean the lubrication system to prevent wear and overheating.
-
Coolant Maintenance: Gas turbines also rely on coolant systems to regulate internal temperatures. Check coolant levels and replace fluids as needed to prevent overheating, which can cause turbine failure.
Vibration and Temperature Monitoring
Vibrations can indicate a number of problems, from unbalanced rotor blades to faulty bearings. Using advanced vibration monitoring systems to detect early signs of issues can prevent costly repairs.
-
Temperature Monitoring: Excessive temperature readings in critical areas can signal underlying issues such as fuel inefficiency or cooling system failures. Regular temperature checks and diagnostic tools can identify potential problems early.
Preventative vs. Corrective Maintenance
A. Preventative Maintenance
Preventative maintenance is the proactive approach of performing routine inspections and tasks to prevent issues before they arise. Tasks like cleaning filters, checking lubrication systems, and inspecting blades are part of this approach.
-
Benefits: Reduces the risk of turbine failure, improves performance, and minimizes operational disruptions.
B. Corrective Maintenance Corrective maintenance occurs when a failure or problem is detected, and repairs are needed. This approach tends to be reactive, and while it can address immediate problems, it is more costly than preventative maintenance.
-
Benefits: Useful for handling unexpected breakdowns, but it often results in expensive repairs and unplanned downtime.
A blend of both approaches is ideal, with a primary focus on preventative maintenance to catch issues early.
Common Gas Turbine Problems and Solutions
A. Excessive Vibration Vibrations can be caused by imbalance in the rotating blades or issues with bearings and rotors. Regular balancing of rotating parts and inspections of bearings can help mitigate this issue.
B. Fuel System Failures Fuel injectors and combustion systems can become clogged or worn over time. Regular cleaning, as well as monitoring fuel quality, helps prevent fuel-related problems that affect turbine performance.
C. Overheating Overheating is a common issue in gas turbines. Ensuring the cooling system is functional and the turbine operates within its optimal temperature range can prevent overheating and potential damage.
D. Contaminant Build-Up Dust, dirt, and corrosion can severely impact performance. Regular cleaning of filters and internal components, as well as ensuring proper sealing of the turbine system, can help mitigate contaminant-related issues.
Role of Digital Tools in Gas Turbine Maintenance
Advancements in digital technology have transformed gas turbine maintenance, bringing new capabilities that significantly improve efficiency and reduce costs. The integration of Condition Monitoring Systems (CMS) and Predictive Maintenance Tools has enabled a shift from traditional reactive maintenance to a more proactive, data-driven approach. Real-time monitoring is one of the key features of these systems. By using sensors, operational conditions such as temperature, pressure, vibration, and airflow can be continuously tracked, providing engineers with instant data on the turbine’s performance. This allows for the early detection of potential issues, helping prevent costly failures before they occur.
In addition to real-time monitoring, data analytics plays a critical role in gas turbine maintenance. By analyzing trends and patterns in operational data, predictive maintenance tools can forecast when specific turbine components are likely to fail. This enables businesses to plan maintenance schedules effectively, replacing parts or making adjustments at optimal times to avoid unplanned downtime. With predictive tools in place, operators can make more informed decisions, leading to cost savings and improved performance over the long term.
Remote monitoring is another game-changing benefit brought by digital tools. With the help of remote diagnostics tools, engineers can monitor turbine conditions from anywhere in the world, improving the speed of response when issues arise. This not only enhances the ability to identify and resolve problems quickly but also reduces the need for on-site inspections and repairs, saving both time and resources. The ability to remotely access turbine data means that maintenance teams can address problems before they escalate, further improving efficiency and reducing the operational impact of turbine failures.
Best Practices for Gas Turbine Maintenance
-
Create a Comprehensive Maintenance Schedule: Establish regular intervals for key tasks like inspections, cleaning, and parts replacements.
-
Use High-Quality Parts and Fluids: Ensure that only high-quality lubricants, filters, and replacement parts are used to maintain the turbine.
-
Train Personnel: Regularly train operators and maintenance staff on best practices for turbine upkeep and troubleshooting.
-
Document Maintenance Activities: Keep thorough records of all maintenance activities, including inspections, repairs, and replacements, to help track turbine health over time.
-
Gas Turbine Control System: The GE Gas Turbine Control System is a cutting-edge solution designed to optimize the performance, safety, and efficiency of GE gas turbines. By integrating advanced sensors, real-time monitoring, and automated control algorithms, the system continuously tracks key parameters such as speed, temperature, fuel flow, and pressure. IS200HFPAG2A, IS200SCTTG1A, and IS215UCVEM06A are examples of GE Gas Turbine Control System spares.
Conclusion
Gas turbine maintenance is an essential aspect of ensuring consistent performance, efficiency, and longevity. By following a comprehensive maintenance plan that includes inspections, cleaning, oil checks, and the use of digital monitoring tools, companies can significantly reduce the risk of breakdowns, enhance operational efficiency, and extend the lifespan of their turbines. Regular preventative maintenance not only saves money in the long run but also ensures that gas turbines remain an integral part of power generation and industrial operations.
What's Your Reaction?
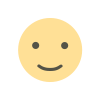
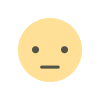


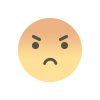
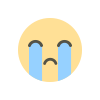
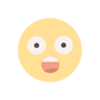