Shell & Tube Heat Exchangers: A Comprehensive Guide

Among the most often utilized heat transfer equipment in commercial settings are shell and tube heat exchangers. From chemical manufacture to power generation, these heat exchangers—known for their dependability, efficiency, and adaptability—are absolutely vital in many kinds of operations. The design, operating concepts, applications, and advantages of shell & tube heat exchangers will be covered in this blog. We will also go over how they may be combined with other systems—such as screw vacuum pumps—to improve performance in different industrial environments.
Definition Of A Shell And Tube Heat Exchanger
A shell and tube heat exchanger is a form of heat transfer mechanism whereby a cylindrical shell encloses a bundle of tubes. One fluid passes through the tubes while the other moves around their exterior. This design lets the two fluids effectively transfer heat without their mingling. Many businesses use these extremely flexible heat exchangers since they can manage high-temperature and high-pressure uses.
Design and Materials: Components
shell
The tube bundle is housed inside an outside cylindrical vessel called the shell. Usually constructed of strong materials like titanium, stainless steel, or carbon steel to resist high temperatures and pressures, it is To guarantee best heat transfer, the shell is made to guide one fluid around the tubes.
Tube Bundles
The tube bundle is made of several tubes set in a particular sequence inside the shell. Usually composed of highly thermally conductive materials, such copper or aluminum, these tubes There are several possible tube configurations; typical forms include triangle, square, and rotating square layouts.
Sheets for Tube Tubes
Thick plates called tube sheets hold the tubes in place and split the shell-side fluid from the tube-side fluid. Usually constructed of materials resistant to corrosion and thermal stress, they are drilled to suit the tubes.
Breads
Installed inside the shell, baffles direct the flow of shell-side fluid and generate turbulence. This improves heat transfer efficiency and keeps fluid flow from causing tubes to vibrate free. Baffles can be fashioned segmentally, helically, or rod-type among other forms.
Outlet and Inlet Nozzles
Opening in the shell and tube sheets, inlet and outlet nozzles enable fluids pass into and out of the heat exchanger. Their meticulously crafted dimensions and location provide ideal flow distribution and reduce pressure drop.
Shell & Tube Heat Exchanger Mechanism
Operating on the thermal conduction principle, shell and tube heat exchangers One fluid runs tube-side—that is, through the tubes—while the other runs around the tubes inside the shell, or shell-side. Via the tube walls, heat moves from the hotter fluid to the cooler one. This process's efficiency relies on elements like surface area, temperature difference, and flow rate.
To improve performance in some systems, shell and tube heat exchangers are coupled with screw vacuum pumps. Vacuum pumps, for instance, can produce a low-pressure environment that enhances heat transfer efficiency in condensation systems or other uses needing exact pressure control.
Shell and Tube Heat Exchanger Applications
Generator of Power
Shell & tube heat exchangers find usage in boilers, condensers, and cooling systems in power plants. Their essential contribution guarantees effective power generation by turning heat energy into electrical energy.
Chemical Conversion
Shell and tube heat exchangers enable chemical facilities to regulate reaction temperatures, condense vapors, and recover waste heat. Maintaining chemical industry process efficiency and safety depends on these equipment.
Industry in Oil and Gas
Shell and tube heat exchangers find usage in the oil and gas industry for liquefaction, gas processing, and refining. Perfect for demanding uses, they manage high-temperature and high-pressure fluids.
HVAC Systems
In heating, ventilation, and air conditioning (HVAC) systems, shell & tube heat exchangers control temperatures and enhance energy efficiency. Large commercial and industrial structures abound in them.
Business of Food and Beverages
Shell and tube heat exchangers find use in the food and beverage sector for sterilization, pasteurization, and cooling operations. They guarantee compliance with safety criteria and good quality of products.
Shell & Tube Heat Exchanger Benefits
Excellent Performance
High heat transfer efficiency is well-known of shell and tube heat exchangers. Their design makes good heat exchange between fluids possible, which qualifies them for many different uses.
Strength
Built from strong materials, shell and tube heat exchangers are quite robust and can survive demanding running environments. Their resistance to mechanical wear, temperature stress, and corrosion guarantees dependability over time.
Flexibility
These very flexible heat exchangers can be tailored to fit certain industrial requirements. Shell & tube heat exchangers can be customized to fit the needs regardless of the high-pressure application or small system size.
Simple Upkeep
Shell and tube heat exchangers' modular design makes maintenance simple. Replacing or cleaning individual parts, including tubes and baffles, helps to lower downtime and maintenance costs by not destroying the whole device.
Difficulties in Shell and Tube Heat Exchanger Design
Fouling
As deposits build on the tube surfaces, fouling results, therefore lowering the heat transfer efficiency. Prevention of this problem and guaranteed best performance depend on regular cleaning and maintenance.
Rusting
Particularly in settings involving harsh fluids, corrosion can affect the integrity of the tubes and shell. One can help to solve this issue by using coatings and corrosion-resistant materials.
Thermal Development
Stress on the tubes and shell brought on by thermal expansion might result in cracks or leaks. Accommodating thermal expansion and guaranteeing dependability of operation depend on good design and material choice.
Development in Shell & Tube Heat Exchanger Technology
Modern Components
Shell and tube heat exchangers now have increased durability and efficiency thanks to the use of sophisticated materials such titanium, nickel alloys, and composites. These materials resist wear, high temperatures, and corrosion better.
Improved Tube Patterns
Heat transfer efficiency has been even improved by tube design innovations including microchannel tubes and finned tubes. These designs raise surface area for heat exchange and boost general performance.
Intelligent Tracking Devices
Real-time shell and tube heat exchanger performance monitoring made possible by sensor and IoT technologies is This guarantees best operating over the lifetime of the equipment, lowers downtime, and helps to enable predictive maintenance.
In conclusion,
Modern businesses depend on shell and tube heat exchangers since they provide great efficiency, durability, and adaptability. Their preferred option in sectors including power generation, chemical processing, and oil and gas is their capacity to manage high-pressure and high-temperature applications.
Shell and tube heat exchangers can improve industrial operations even more when combined with complementary equipment such as screw vacuum pumps, therefore guaranteeing dependability and best performance. These tools will become more crucial in determining the direction of sustainable and energy-efficient businesses as technology develops.
Understanding the design, uses, and advantages of shell and tube heat exchangers helps companies to make wise selections and maximize these tools to meet their running objectives. Modern industrial innovation is mostly based on shell and tube heat exchangers, whether they improve process efficiency or lower environmental impact.
What's Your Reaction?
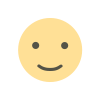
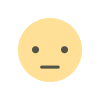


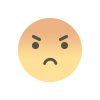
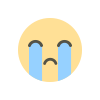
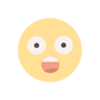